Detail Author:
- Name : Cielo Buckridge
- Username : maggie.davis
- Email : tzieme@hotmail.com
- Birthdate : 1998-03-29
- Address : 6435 Boyle Causeway Funkburgh, WI 49866
- Phone : (319) 332-0079
- Company : Bartell-Weber
- Job : Airframe Mechanic
- Bio : Sed ullam nihil est quo. Corrupti recusandae delectus sit explicabo consequuntur. Explicabo modi ut quia debitis ad.
Socials
instagram:
- url : https://instagram.com/boganr
- username : boganr
- bio : Ipsa nulla ut vero ut error non. Non ratione quo maiores cumque.
- followers : 177
- following : 32
facebook:
- url : https://facebook.com/ruth_official
- username : ruth_official
- bio : Qui tempore eum dicta aperiam. Est unde dolores esse minima ut quia et et.
- followers : 142
- following : 449
tiktok:
- url : https://tiktok.com/@ruth_bogan
- username : ruth_bogan
- bio : Assumenda soluta totam aliquam nesciunt et earum.
- followers : 341
- following : 2602
twitter:
- url : https://twitter.com/ruth.bogan
- username : ruth.bogan
- bio : Enim voluptatem reiciendis repellat. Ab ut est sed quos quis ratione. Alias voluptatem consequuntur sint.
- followers : 269
- following : 1339
linkedin:
- url : https://linkedin.com/in/ruthbogan
- username : ruthbogan
- bio : Qui quis ducimus saepe sequi deserunt.
- followers : 3043
- following : 1414
It can feel pretty frustrating, you know, when you are trying to make something work in your design program, and a basic piece just won't behave. Sometimes, it seems like the software just can't quite "see" or pick out the specific surface you want to work with. You're trying to build something, maybe a new part or a detailed piece for a project, and the computer acts as if that particular section of your model simply isn't there, or it's not the right kind of thing to touch. It's a bit like trying to point to something on a map and the map just showing you a blank spot where your finger is.
This kind of snag, where the program has trouble recognizing or handling a specific part of your creation, can really slow things down. It's not just about a small hiccup; it can stop your progress cold. You might be trying to make a copy of a whole setup, or perhaps you're just attempting to shape a simple curve, and suddenly, the program tells you it doesn't have a good way to refer to the bit you're pointing at. It feels, in a way, like the digital tools are losing their grip on what they're supposed to be doing.
So, what's going on when your design software seems to lose its ability to "identify" or properly interact with the surfaces of your three-dimensional shapes? We hear from folks who run into these sorts of issues all the time, from trying to make a simple bucket to getting complex parts to fit just right. It's a common stumbling block for many who spend their days building things in a digital space. We will explore some of these common headaches and, you know, maybe shed a little light on why these digital surfaces can be so stubborn.
Table of Contents
When 3D Faces Just Won't Cooperate
Why Does Face Identification Not Working Happen with Copies?
Copying Troubles and Unseen References
Is Your Software Struggling to Grab the Right Face?
Exporting and Selecting When Face Identification Not Working
What Makes Face Identification Not Working During Modeling?
Shaping Surfaces and Tricky Splits
Facing Display and Orientation Glitches?
Flipping and Placing Issues with Face Identification Not Working
When 3D Faces Just Won't Cooperate
Picture this: you're working on a new design, maybe for a building or a product, and you've put together a family of parts that rely on a flat surface to attach themselves. Everything seems pretty good when you first put that family together with its main object. It clicks right into place, and the software seems to know exactly what's what. But then, you make a duplicate of that whole arrangement, and suddenly, the new copy starts acting a little funny. The parts in the duplicate group, well, they just don't seem to recognize their host surface anymore. It's almost as if the program loses its way trying to figure out what surface belongs to what, especially when it comes to getting a proper handle on that surface's location or characteristics. This can be, you know, a real head-scratcher, making you wonder if the surface you're trying to grab needs to belong to a different part of your project altogether for the program to truly "see" it.
This sort of thing isn't just limited to copying groups. Sometimes, you might be trying to pull a specific surface out of a solid shape you've made, perhaps to send it off to another program or to use it for something else. You've even gone to the trouble of giving that surface a special name, hoping the program will easily find it. But even with a name, the software just can't seem to get a proper hold of it for the export. It's like you've given it a label, but the program still can't quite pick it out of a crowd. This can be rather annoying, especially when you're trying to move your work between different tools or save a particular piece of your model for later use.
Then there's the situation where you're just trying to move things around. Imagine coming from one design program to another, and you're used to a certain way of doing things. You want to shift a whole object, or maybe just a tiny point, or even just one of those surfaces, and you just can't find the simple way to do it. You know there's a way to get it done, perhaps by changing how the program looks at collections of curves, but it feels like you're fighting the basic act of getting something to slide from one spot to another. It's a fundamental action that, you know, should be straightforward, but the program just doesn't make it easy to grab and move that particular piece.
Why Does Face Identification Not Working Happen with Copies?
When you take a finished piece of your design, like a family of objects that all connect to a main surface, and then you make a copy of that whole arrangement, sometimes the new copy just doesn't behave. It's as if the program forgets how to properly "see" or connect to the original surface reference in the duplicate. You might find that the copied objects are there, but they don't seem to understand their relationship to the surface they're supposed to be sitting on. This happens because, you know, the way the program keeps track of these surface connections can get a little mixed up when things are duplicated. It's almost like the new copy doesn't inherit the proper instructions for how to find and link up with its base surface, causing a sort of digital amnesia where the necessary reference just isn't valid anymore.
Copying Troubles and Unseen References
So, what exactly goes wrong when you try to copy a group and suddenly your face identification not working becomes an issue? It often comes down to how the software handles the underlying instructions that tell a part where its "host" surface is. When you duplicate a group, the program tries to recreate all those connections. But sometimes, especially with complex arrangements or specific types of families, the new connections don't quite point to a proper, usable surface. The system might have been looking for a very specific type of surface that belongs to another original part, and the copied version just doesn't provide that exact match. It's a bit like trying to use a map that only works for the original location, and when you copy the map, it doesn't update for the new spot. This can lead to a lot of head-scratching when your carefully placed elements suddenly seem to float or lose their connection to the main model, simply because their copied "face" reference isn't something the program can properly interpret or use. You might even wonder if the surface you're trying to connect to needs to be part of a different, more fundamental piece of the original design for the program to properly recognize it in the copy.
Is Your Software Struggling to Grab the Right Face?
Have you ever found yourself trying to pull a single surface out of a complex shape, perhaps to save it as a separate file or use it in another part of your project, and the program just won't let you? You might have even given that specific surface a special name, thinking that would make it easier for the software to pick it out. But even with a clear label, the program seems to have trouble getting a proper hold of it for things like exporting. It's like the software knows the surface is there, but it can't quite "grab" it in a way that makes it usable for the next step. This can be very frustrating, especially when you're trying to get a specific piece of your model to move from one place to another, or to convert it into a different format. It feels, you know, like a very basic task, but the program just isn't cooperating.
Exporting and Selecting When Face Identification Not Working
When your design program has trouble with face identification not working during exporting or selecting, it can really throw a wrench into your workflow. Imagine trying to export just one specific surface from a solid shape, perhaps as a DXF file, using a tool that's supposed to automate these kinds of tasks. You've even gone to the trouble of making that surface a "named entity," giving it a clear label so the program should easily find it. Yet, the software struggles to actually pull that named surface out. It's almost as if, despite the name, the program can't quite pinpoint the exact boundaries or properties of that surface in a way that allows it to be exported cleanly. Similarly, when you're working in a program like Maya and you try to select a whole or even a partial loop of surfaces by double-clicking, the software might just pick the wrong set. It's a common issue where, if there are two possible paths for the loop, the program just doesn't make the correct choice, leaving you with an unexpected selection. This kind of misidentification can make even simple tasks, like selecting a series of connected surfaces, a surprisingly difficult chore.
What Makes Face Identification Not Working During Modeling?
When you're trying to build something from scratch, like a bucket, and you start by shaping a cylinder and pulling out its sides, you expect to get a complete object. But then you realize you don't have an inner wall, and you're left wondering how to create it. You might try to connect two edges, hoping to bridge the gap and form that missing surface, but the program just tells you that the meshes are being bridged, without actually completing the action. This is a pretty common spot where face identification not working pops up, because the software isn't correctly interpreting how those edges should connect to form a new surface. It's a bit like trying to close a zipper, but the teeth just won't interlock properly to form a continuous line. This can be a real roadblock when you're trying to create a hollow shape or add thickness to an existing surface, because the basic tools for making new surfaces just aren't doing what they're supposed to do.
Shaping Surfaces and Tricky Splits
Creating specific shapes and cutting objects can become surprisingly difficult when the software struggles with face identification not working. For instance, if you're trying to add a very precise, narrow groove to a part's surface, perhaps just 3mm wide, using a simple plunge motion, the program might not let you. Or, if you try to use a contour turning method on that same surface with a grooving tool, it just doesn't seem to work. It's as if the software can't quite grasp the exact dimensions or the specific path needed to carve that groove into the surface. This happens because the program isn't accurately "seeing" or processing the surface's properties in relation to the tool's movement. Similarly, imagine having a solid object and wanting to slice it into multiple pieces along a curved surface. You want to end up with three distinct parts after the cut, but getting the software to accurately follow that curved surface for the split can be a real challenge. It's like trying to cut a cake with a wavy knife, but the knife just doesn't follow the curve, leading to an uneven or incomplete separation. These are moments when the software's ability to precisely identify and interact with surfaces becomes absolutely critical, and when it falters, even simple shaping tasks become frustratingly complex.
Facing Display and Orientation Glitches?
Sometimes, the issue isn't even about creating or moving surfaces, but simply getting them to look right. If you're working in a program like Maya, and the menu for adjusting how surfaces are oriented (their "normals") has been removed from the quick access tools, you might find yourself scratching your head trying to figure out how to flip a surface. You just want the surface to show the correct side, to appear gray instead of black, which indicates it's facing the right way. But without that easy access, it's a puzzle to get the program to properly recognize and adjust which side of the surface is "out." It's a bit like trying to turn a page in a book, but the page just keeps showing you the back. This is a pretty common problem where the visual representation of the surface, which relies on the program's understanding of its "face," just isn't cooperating.
Flipping and Placing Issues with Face Identification Not Working
When you're dealing with issues like surfaces showing up black instead of gray, or objects not orienting correctly, it often points to a problem with face identification not working in terms of display or placement. In some programs, simply telling a fixture to "place on face hosting" will magically flip it to the correct direction in your ceiling plan. This works because the program understands the relationship between the object and the surface it's sitting on, using that "face" as a guide for its orientation. However, if you're trying to do this without using a specific view, like a reflected ceiling plan, the best way to get it right might involve drawing a special reference line from an elevation view. This extra step is needed because the program isn't automatically figuring out the proper "up" direction based on the surface alone. Moreover, sometimes you want to pull a curved surface straight out, without changing its bend. For example, if you have a dish with a gentle curve, and you grab its inner surface, you want to extend it without making the curve any tighter or looser. But the software might struggle to keep that original curve exactly the same while extending it in a straight line, as if it can't quite "remember" the original bend of the surface as it stretches. This kind of difficulty shows how the program's precise understanding and manipulation of a surface's properties are crucial for getting things to look and behave just as you intend.
These issues, from objects losing their connection to a surface when copied, to programs struggling to export a named surface, to difficulties in creating inner walls or specific grooves, and even to simply getting surfaces to display or orient correctly, all stem from the core challenge of "face identification not working." It's about the software's ability to accurately recognize, reference, and manipulate the distinct surfaces of your three-dimensional creations. Whether it's a problem with how references are handled during duplication, how specific surfaces are selected for export, how new surfaces are formed during modeling, or how existing surfaces are displayed and oriented, these are common frustrations for anyone building in a digital space. Sometimes, too, when you get a file that's just a mesh, like an STL, and you want to turn it into a solid object you can change, the program might struggle if the object has lots of surfaces that are supposed to be connected. And then there's the odd case where, when you try to pick a series of connected surfaces by double-clicking, the program just chooses the wrong path for the selection. These are all variations of the same fundamental problem: the digital tools just aren't quite "seeing" or understanding the surfaces the way you need them to.

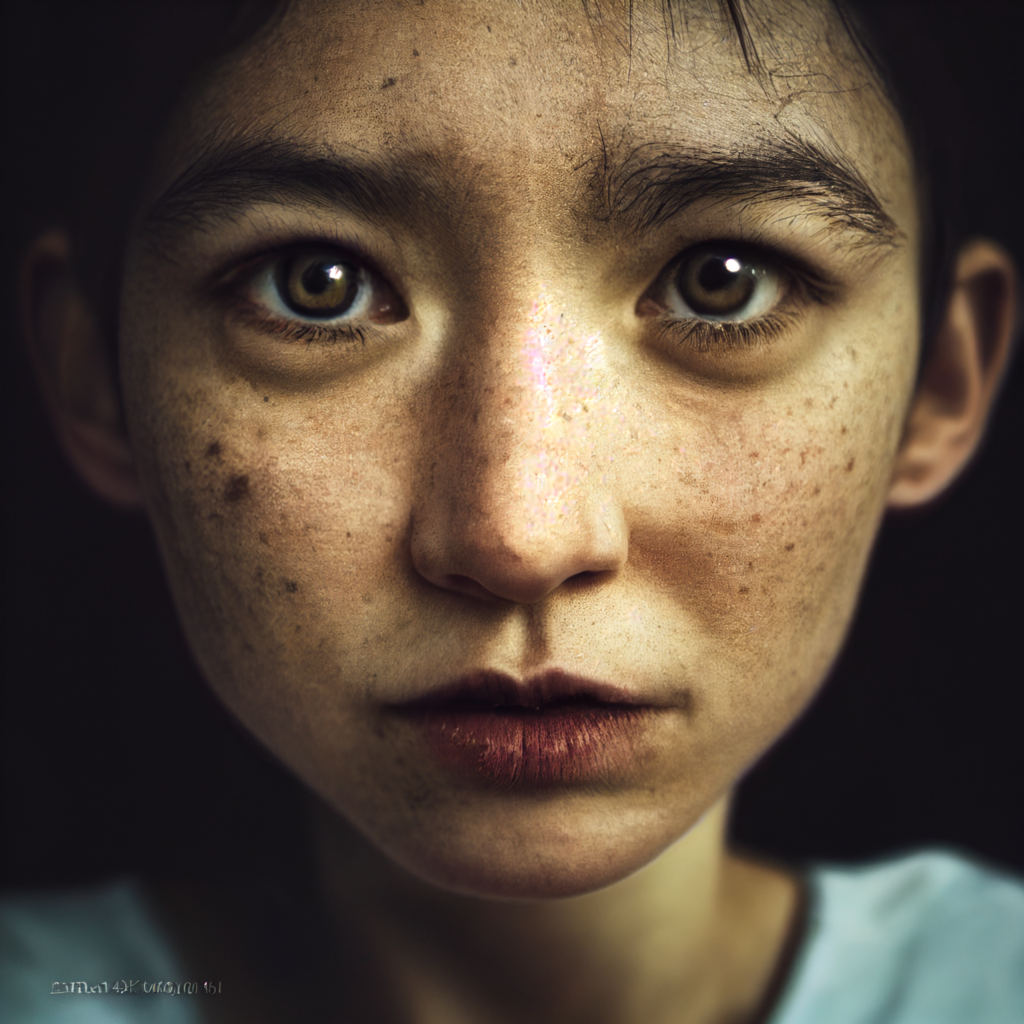
